Установки для нанесения вакуумного напыления представляют собой оборудование, предназначенное для создания тонких покрытий. Суть используемой технологии заключается в следующем: в вакуумной среде происходит прямая конденсация пара, который содержит частицы наносимого вещества, на поверхности обрабатываемого изделия.
Принцип и основы технологии вакуумного напыления
Суть данной методики состоит в том, что при помощи специального оборудования образуется поток микрочастиц наносимого материала, а после их конденсации на его поверхности создается пленка. Но первым делом нужно обеспечить переход напыляемого вещества в газовую форму, затем – перенос частиц к поверхности, которую необходимо обработать. Также требуется создать необходимые условия для их. Для этих целей используют специальное профессиональное оборудование.
Установки вакуумного напыления предназначены для следующих случаев:
- когда необходимо нанести функциональное покрытие с уникальными параметрами (например, с повышенной износостойкостью, с устойчивостью к коррозии или эрозионным процессам, с антифрикционными или барьерными свойствами);
- для создания оптических покрытий с фильтрующими или отражающими свойствами;
- при производстве микроэлектроники (с ее помощью формируются проводящие слои);
- для создания декоративных покрытий в ювелирных изделиях.
С использованием данной технологии обрабатываются чаще всего изделия из алюминия, молибдена, хрома. В некоторых случаях во время напыления в рабочей камере используется химически активный газ, например, ацетилен или азот.
После окончания процесса вакуумного напыления дополнительная обработка поверхности не нужна.
Вакуумные напылительные установки: виды и особенности устройства
У нас вы можете заказать напылительные установки разных типов, которые можно использовать в прецизионной оптике, микроэлектронике, ювелирном деле и других областях. Возможны также разработка и изготовление универсальных установок, которые будут решать широкий круг задач.
Но, несмотря на то, что установки вакуумного напыления бывают разных типов, все они включают одни и те же основные элементы:
- Рабочая камера, в которой и происходит напыление. Обычно она делается из прочной нержавеющей стали. При необходимости дверь в камеру можно оборудовать смотровыми окнами.
- Вакуумная откачная система, благодаря которой внутри камеры создается вакуум. Эту систему оборудуют турбомолекулярным насосом, безмасляным механическим насосом и крионасосом
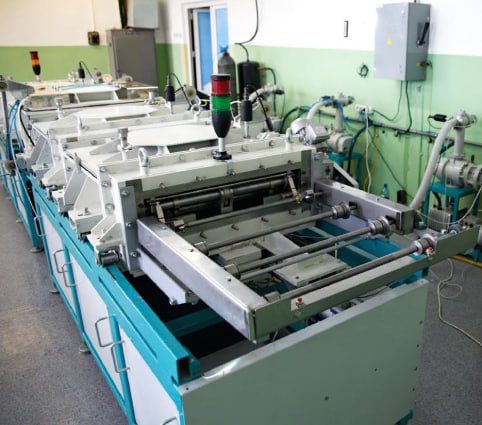
- Система подачи газа и его распределения отвечает за организацию газового потока и подачу его к магнетронному источнику. Она состоит из клапанов, «ловушек» и средств для измерения и удобного регулирования скорости потока.
- Электронно-лучевой испаритель имеет надежный источник питания, компактный блок управления, механизм поворота тиглей и термический испаритель.
- На подложкодержателе располагается обрабатываемый материал.
- Система электропитания для всех рабочих узлов установки.
- Система контроля показателей вакуумного напыления, которая позволяет задавать скорость процесса, температуру отжига и обрабатываемой поверхности, толщину готовой пленки. Также существует возможность контроля физических свойств покрытия за счет специализированных датчиков.
- Транспортирующие устройства предназначены для ввода и вывода обрабатываемых изделий в вакуумную камеру.
- Вспомогательные устройства и технологическая оснастка: разнообразные заслонки и экраны, устанавливаемые внутри камеры, системы для очистки газа и т.д.
- Установки для напыления декоративного или оптического покрытия могут отличаться от универсального варианта размерами камеры, типом насосов, используемых вакуумной откачной системы, но в целом они работают по такому же принципу, и включают те же основные компоненты.
- Управление работой вакуумных установок осуществляются с помощью лицензионного программного обеспечения, которое поставляется вместе с оборудованием и устанавливается на отдельный компьютер.
Как работают вакуумные напылительные установки
Работа оборудования вакуумного напыления состоит из следующих этапов:
- Создание вакуума в камере, получение пара из частиц вещества, которое формирует напыление.
- Транспортировка деталей или изделий в рабочую камеру, где их располагают на строго определенной позиции.
- Распыление материала, из которого будет создаваться пленка. В ходе этого процесса пар конденсируется на подложке, и в итоге формируется покрытие с заданными свойствами.
Наши предложения по технологиям вакуумного напыления:
- отрезающие коротковолновые и длинноволновые фильтры (покрытия) для УФ, ВД и ИК диапазонов спектра (по ТЗ заказчика);
- полосовые и узкополосовые фильтры для всех диапазонов спектра (по ТЗ заказчика);
- просветляющие покрытия для всех диапазонов спектра (по ТЗ заказчика);
- поляризационные покрытия (по ТЗ заказчика);
- светоделительные покрытия (по ТЗ заказчика);
- критические технологии:
- сверхширокополосное просветляющее покрытие (R = 0,3 ÷ 0,5 % для λ = 400 ÷ 1100 нм);
- сверхглубокое просветление (R = 0,05 ÷ 0,1 % для λ = 420 ÷ 700 нм);
- сверхтолстые металлические покрытия (Cu, Ni и др.) на стекле и металлах (d = 50 ÷150 мкм);
- просветляющие покрытия для лазерных длин волн повышенной лучевой прочности (по ТЗ заказчика);
- лазерные зеркала для УФ, ВД и ИК диапазона повышенной лучевой прочности (разработка технологии по ТЗ заказчика, внедрение или создание установки);
- высокоотражающие металл-диэлектрические зеркала высокой прочности (R = 95 ÷ 97 % для λ = 400 ÷ 700 нм и λ = 700 ÷ 1100 нм);
- просветляющие покрытия для ИК-диапазона повышенной прочности (двойная нулевая группа прочности / 10.000 оборотов с нагрузкой 200 г): T = 95 % для λ = 7,5 ÷ 13 мкм — двойная нулевая группа прочности; T = 98 ÷ 99 % для λ = 8 ÷ 13 мкм — двойная нулевая группа прочности;
- аналогичные покрытия для 1-го окна прозрачности атмосферы (λ = 3 ÷ 5 мкм);
- прочное просветляющее покрытие (двойная нулевая группа) для λ = 3 ÷ 13 мкм (T > 60 %), Tmax = 98 ÷ 99 % для 7 ÷ 10 мкм (двойная нулевая группа прочности);
- твердоуглеродные, алмазоподобные, алмазные пленки (по ТЗ заказчика);
- износостойкие покрытия (по ТЗ заказчика);
- токопроводящие покрытия (по ТЗ заказчика);
- алмазоподобные покрытия на медицинские инструменты;
- биосовместимые покрытия на импланты и протезы;
- нанесение вакуумных покрытий с одновременной подполировкой деталей до улучшения качества поверхности деталей с покрытием до 4-го класса по ГОСТ2789-59 или получения шероховатости с Ra до 0,005 по ГОСТ2789-73.